What is ICS (Industrial Control System) Security?
What is ICS (Industrial Control System) Security?
Industrial Control System (ICS) Security is dedicated to safeguarding the integrity and functionality of industrial control systems. This encompasses both the hardware and software components used by these systems and their operators.
ICS primarily manages and operates essential infrastructure-supporting functions such as water supply, power generation, transportation, manufacturing, and other critical services. As these systems increasingly rely on digital technology, including software, computers, endpoints, and networks, it becomes crucial to secure them to ensure the safety of the system, its operators, and the people it serves.
How ICS Security Works?
The primary goal of ICS security is to protect the machinery's operational processes from cyber threats. In situations where worker or public safety is at risk following a security event, there may be provisions for immediate assistance through an ICS security contact.
Efficiency in ICS management is also a key aspect of ICS security. This often involves ensuring comprehensive visibility into machinery operations, typically monitored from a control room or center equipped with detailed dashboards that provide critical operational data.
Why is Cybersecurity Important for ICS?
Cybersecurity in the context of ICS is vital because it directly impacts the physical safety of both the workers involved and the general public who rely on these services.
Inadequate ICS security can lead to disruptions in essential services for the public. Furthermore, there is a significant risk of physical harm to employees if industrial machinery were to malfunction due to security breaches.
Effective ICS security ensures smooth and efficient operations, safeguarding both infrastructure and operational continuity whereas operational downtime due to a cyber incident can cost organizations severe financial consequences.
What is the Difference Between ICS and OT?
While the terms OT and ICS are sometimes used interchangeably, there are key differences. ICS is a significant subset of OT, specifically focused on monitoring and controlling industrial processes. These systems typically utilize specialized protocols and hardware designed for industrial settings.
OT, in contrast, is a broader term that encompasses all hardware and software used in managing and controlling industrial processes, including ICS. Beyond ICS, OT encompasses systems like Supervisory Control and Data Acquisition (SCADA) systems and Distributed Control Systems (DCS), among other technologies. These systems are designed for reliability, security, and resilience and often require specialized expertise for implementation and maintenance. In essence, while all ICS are forms of OT, not all OT systems are classified as ICS.
Examples of Industrial Control Systems
Industrial Control Systems (ICS) are crucial in various sectors due to their extensive applications in managing and controlling industrial processes. Two common examples of ICS are:
1. Supervisory Control and Data Acquisition (SCADA) Systems
Functionality: SCADA systems are a blend of software and hardware elements that provide control at the supervisory level. They enable industrial organizations to manage processes both locally and remotely, monitor and gather real-time data, and interact with field devices like sensors, valves, pumps, and motors using Human-Machine Interface (HMI) software. These systems also log events for record-keeping.
Applications: SCADA systems are extensively used in industries for remote monitoring and control of field sites via centralized systems. They are prevalent in pipeline monitoring and control, water treatment and distribution, and electrical power transmission and distribution.
Advantages: They offer cost reduction, flexibility, and enhanced performance efficiency.
Security Risks: With the rise in remote access and internet connectivity, threats to these systems have increased. In extreme cases, such as hacking, adversaries can gain control over critical infrastructure like water supplies, electrical grids, or even nuclear reactors, underlining the importance of robust ICS security.
2. Building Management Systems (BMS)
Functionality: BMS are computer-based systems designed to control and monitor various building management aspects. They are focused on ensuring the safety of facility operations, optimizing performance, and reducing energy consumption.
Applications: BMS systems manage HVAC, lighting, energy management, security, fire and life safety systems, and elevator and escalator systems. They are pivotal in enhancing operational efficiency, occupant comfort, safety, and reducing operating costs and environmental impact.
Critical Use Cases: In healthcare delivery organizations (HDOs), for instance, BMS plays a vital role in patient safety.
Security Risks: Cyberattacks on BMS can lead to severe consequences, ranging from disruption of critical manufacturing processes and data theft to compromising patient safety in hospitals.
These examples illustrate the diverse nature of ICS across various industries. Regardless of their specific applications, all ICS share a common need for comprehensive security strategies to protect against the inherent challenges and threats they face in today's increasingly connected world.
ICS Security Challenges
The security of Industrial Control Systems (ICS) is fraught with several challenges, each demanding specific attention and strategies to ensure robust protection. Key challenges include:
1. IT/OT Convergence
Issue: The merging of Information Technology (IT) and Operational Technology (OT) systems, once managed separately, poses significant security challenges. This convergence enhances overall integration and supply chain visibility, but it also broadens the attack surface, making systems more vulnerable to cyberattacks.
OT Infrastructure Risks: Many OT infrastructures are inadequately protected against cyber threats. Traditional IT security tools often are incompatible with OT environments, as they might disrupt critical processes, leading to production loss or safety hazards.
2. Legacy Systems
Problem: A large number of industrial control systems are outdated, having been designed decades ago without contemporary security features like encryption and authentication. This leaves them particularly vulnerable to cyberattacks.
Security Features Gap: The absence of modern security measures in these legacy systems presents significant risks in the current cyber threat landscape.
3. Remote Access
Access Control Issues: Insufficient access control mechanisms in many ICS environments make it easier for cybercriminals to gain unauthorized access.
Challenges with External Users: The need for internal and third-party remote access to industrial assets complicates security, especially for third-party users who may not have shared infrastructure, increasing cost and complexity.
Impact on Operations: Without secure and controlled remote access, visibility into operational activities is limited, affecting uptime and safety. The lack of centralized monitoring systems further hampers the ability to detect and respond to cyber incidents.
4. Patching
Downtime Intolerance: The inability to afford downtime in many industrial settings means that maintenance windows are rare. This leaves systems exposed to known vulnerabilities that could be exploited in cyberattacks.
5. APT Attacks
Targeted Cyberattacks: ICS are often the focus of sophisticated cyberattacks like Advanced Persistent Threats (APTs). These threats are characterized by their stealth and persistence, designed to remain undetected over long periods, thereby inflicting significant damage to critical infrastructure.
Custom-Made Tools: APT actors often develop specialized tools targeted at ICS, making these systems challenging to defend without a comprehensive security strategy.
Common ICS Threats
The industrial landscape has evolved significantly from a time when machinery lacked computational capabilities and was impervious to remote cyber threats. Today, several critical threats are prevalent in this space.
External Threats and Targeted Attacks
Industrial processes are integral to public health and quality of life, making them prime targets for various malicious entities like terrorists, hacktivists, and malicious insiders. These actors might seek to disrupt operations or steal data by:
- Interrupting Key Operations: Even brief disruptions can have widespread impacts.
- Exfiltrating Data or Intellectual Property: Aimed at gaining unlawful access to sensitive information or disrupting production to cause harm.
A defense-in-depth strategy is crucial to shield vital systems from these threats.
Internal Threats
ICS systems often lack robust authentication controls, making them vulnerable to internal threats. A single individual with access could potentially compromise multiple machines and systems, causing significant damage. Risks include:
- Introduction of Malware: Leading to the halting of production.
- Data Theft: Exploiting access to internal databases to exfiltrate large volumes of sensitive data.
Click to learn more about Insider Threats (“The truth behind OT insider threats”)
Human Error
Mistakes like incorrect equipment configuration, programming errors, or missing alerts can significantly disrupt operations. These errors are often due to inexperienced individuals handling complex systems, leading to costly oversights.
ICS Security Best Practices
Implementing robust security practices is vital for protecting ICS environments:
- Perform ICS Asset Discovery: Full visibility into the ICS infrastructure is essential for comprehensive security.
- Monitor Network Baselines: Establish and monitor network baselines to detect anomalies or unauthorized device connections, as ICS networks are typically stable with few changes in connected devices.
- Perform Network Segmentation: Replace traditional air-gapped networks with segmented networks using firewalls that understand ICS protocols, as many systems are now connected to the Internet.
- Implement Least Privilege: Use ICS protocol-aware firewalls to enforce access controls, especially since many ICS protocols lack native access control mechanisms.
- Deploy an Intrusion Prevention System (IPS): An IPS helps identify and block exploitation attempts on known vulnerabilities in ICS systems and their legacy operating systems.
- Secure Remote Access: Implement strong authentication, access control, and encryption for remote access to monitor and manage geographically distributed ICS assets.
- Secure Physical Access: Physical security measures are as crucial as cyber security measures to protect ICS assets and prevent bypassing of defenses.
Components of an ICS Environment
An Industrial Control System (ICS) environment comprises several critical components, each playing a unique role in managing and controlling industrial processes. Key components include:
- Supervisory Control and Data Acquisition (SCADA) systems effectively administer and oversee dispersed equipment in industrial settings.
- Distributed Control Systems (DCSs), akin to SCADA systems, are responsible for the management and surveillance of industrial assets and operations.
- Programmable Logic Controllers (PLCs) are key elements within the ICS framework, widely employed in the automation of industrial activities and in gathering information for analytical purposes and enhancing industrial efficiency.
- Human-Machine Interfaces (HMIs) serve as graphical interfaces that facilitate interaction between humans and ICS devices and procedures.
- Sensors play a crucial role in gauging various industrial parameters, including but not limited to temperature, pressure, humidity, and flow rate.
- Actuators take in information from sensors and PLCs, along with other ICS components, and subsequently execute control over physical processes in accordance with the analyzed data they receive.
Industrial Control Systems FAQs
What is an ICS network?
An Industrial Control System (ICS) network connects various ICSs, enabling them to communicate and collaborate to improve security, efficiency, and safety.
What is SCADA?
Supervisory Control and Data Acquisition (SCADA) is a control system architecture that employs computers, networked data communications, and graphical user interfaces for high-level supervisory management of processes. It also integrates other peripheral devices, such as programmable logic controllers and discrete PID controllers, to interface with process plants or machinery.
How Darktrace provides OT security
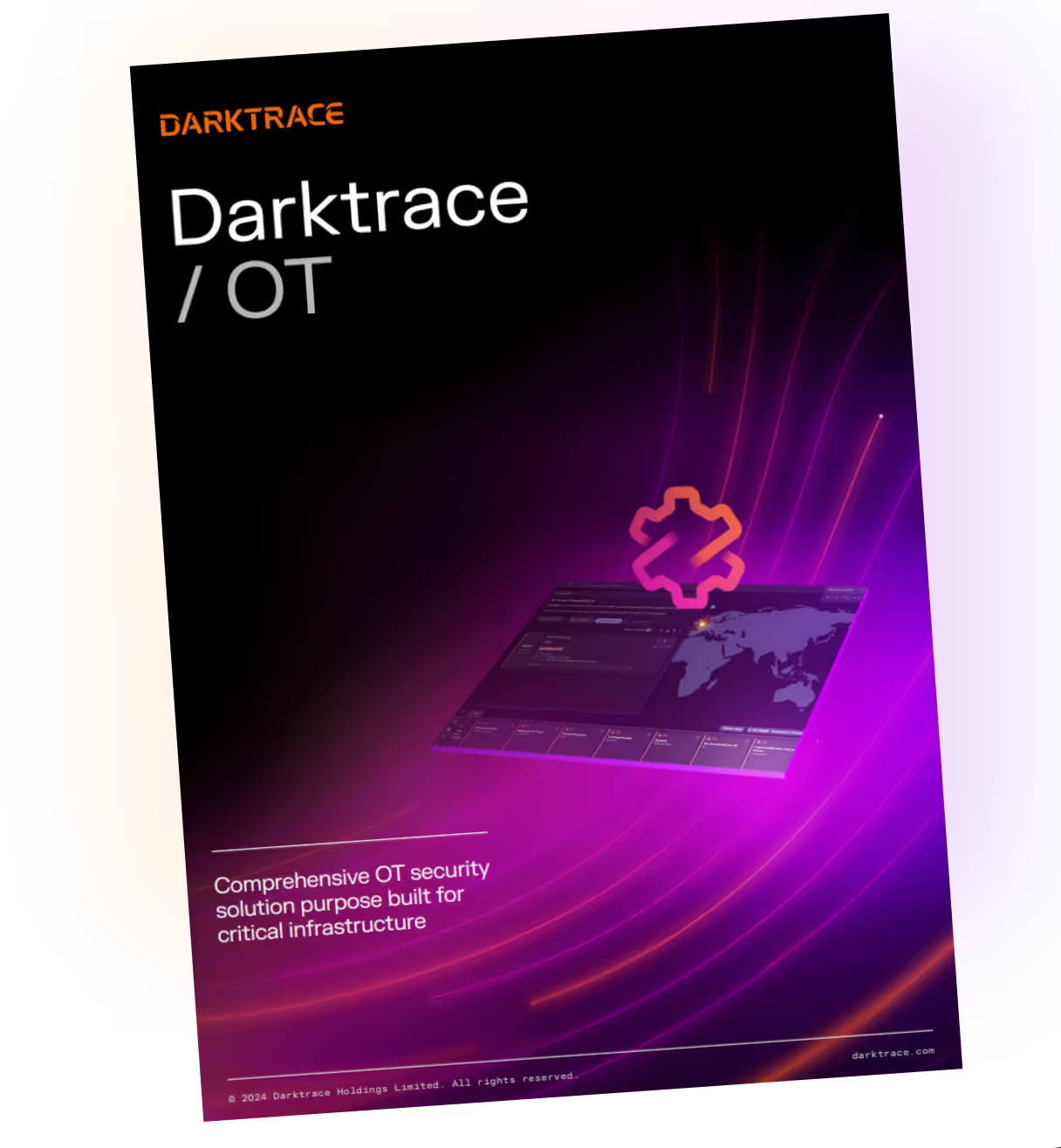
Darktrace / OT is a comprehensive security solution built specifically for critical infrastructure. It implements real time prevention, detection, and response for operational technologies, natively covering industrial and enterprise environments with visibility of OT, IoT, and IT assets in unison.
Using Self-Learning AI technology, Darktrace / OT is the industry's only OT security solution to scale bespoke risk management, threat detection, and response, catching threats that traverse network- and cloud-connected IT systems to specialized OT assets across all levels of the Purdue Model.
Instead of depending on knowledge gained from past attacks, AI technology learns what "normal" usage is for its environment and identifies previously unknown threats by detecting slight pattern variations. This gives engineering and security teams the confidence to evaluate workflows, maintain security posture, and effectively mitigate risks from a unified platform in less time.